Reoil is Europe’s largest plant processing end-of-life tyres in a globally unique continuous pyrolysis process.
The company has the know-how, technology, experienced engineering and research staff with its R&D department and the potential necessary for new investments.
The Company has partnered with Zeppelin System AG to build further facilities to recycle end-of-life tyres.
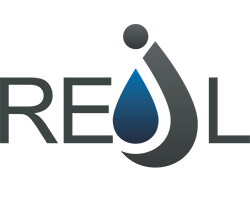
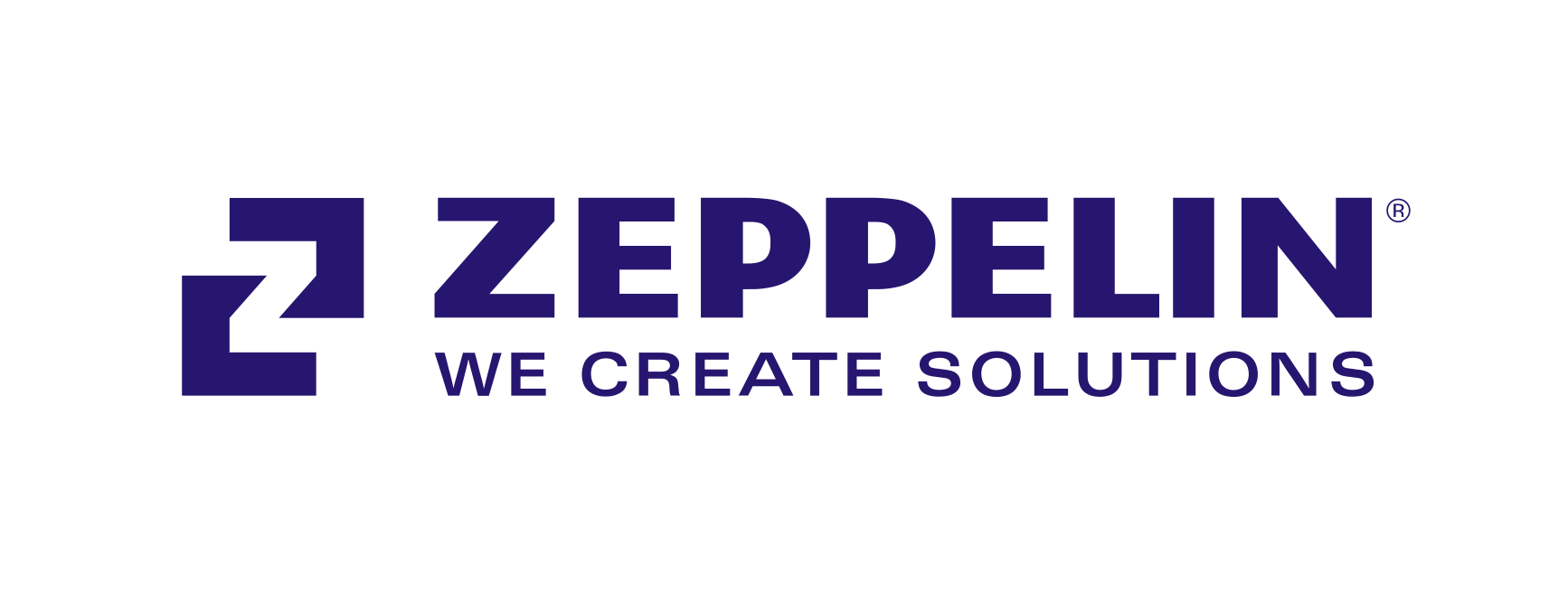
Currently, the Company’s top priority is constructing a second plant with a capacity of 60.000 tons of end-of-life tyres a year and realising several installations worldwide.
The projects are being carried out jointly with Zeppelin Systems AG under the EPC ‘turnkey’ formula, covering the full scope of design, construction and commissioning.
Continuous pyrolysis technology
Continuous pyrolysis, through complete control of the process system, enables optimum use of energy and raw materials, while stabilised production allows for consistent product quality. The continuous pyrolysis process is characterised by high efficiency while minimising costs.
Products in the recycling process
Pyrolysis oil (TPO)
8600 tons / year
Carbon black (rCB)
6400 tons / year
Carbon black (recovered Carbon Black – rCB) is used to manufacture tyres and other industrial rubber products. It increases the mechanical strength of the compound. Thanks to its colouring properties, it is also used to produce dyes.
Steel
2600 tons / year
Cleaned and remelted, it can be reused. The steel used for tyre production is classed as high-quality special steel. Steel cord is distinguished by its extremely low textile and rubber inclusions content.
Textiles
400 tons / year
Contribution to Environmental Protection
The unique features and key technological developments of pyrolysis processes help protect the environment while contributing to solving the problem of disposing of end-of-life tyres.
The continuous pyrolysis technology developed by Reoil enables gas emissions to be minimised and all the site's environmental requirements to be met.
50.000 tons
GHG greenhouse gas emissions saved per year per plant
80% less
GHG emissions in carbon black production (rCB) compared to traditional methods
94% less
GHG emissions in the production of TPO in relation to the use of fossil fuels
Recycling
of steel reducing 80% of CO2 emissions, 75% of pollution
and 40% of water consumption
Decomposition
of tyres in an oxygen-free atmosphere does not require combustion and does not generate combustion products
Emission
of harmful substances below the permissible standards
Autothermal
production process with minimal energy consumption
Closed cycle
of life of raw materials and products